El mantenimiento preventivo ya no es un sector cuyo trabajo se reduce a “apagar incendios”. Hoy, su desempeño en la industria marca la diferencia en los resultados de producción.
Por ello, es fundamental hacer del mantenimiento de los equipos una herramienta que genere valor para el negocio.
En este sentido, la creación de rutinas de mantenimiento preventivo se ha convertido en una fuerte tendencia. Sin embargo, no todos saben por dónde empezar o si vale la pena invertir en este cambio de estrategia.
Para despejar dudas sobre el tema, explicaremos aquí las ventajas de este tipo de mantenimiento, cómo funciona su aplicación, la diferencia con relación a otros mantenimientos, además de compartir valiosos tips para su implementación.
¡Disfruta leyendo y descubre por qué el método preventivo es el mayor aliado de tu negocio!
¿Qué es el mantenimiento preventivo?
El mantenimiento preventivo engloba todas las acciones que se realizan periódicamente para prevenir cualquier tipo de falla o daño en los equipos.
Este tipo de revisión está prevista en la NBR 5462/94, que define la estrategia como el mantenimiento realizado en intervalos programados o con criterios específicos.
Además del mantenimiento preventivo, existen otros dos tipos de mantenimiento descritos en las normas de la ABNT (Asociación Brasileña de Normas Técnicas): predictivo y correctivo.
Hablaremos más de cada uno de ellos a lo largo de este artículo, pero antes, entendamos la importancia del proceso preventivo para la conservación y rendimiento de las máquinas.
¿Cuál es el propósito del mantenimiento preventivo?
El principal objetivo de esta estrategia es precisamente actuar en prevención para evitar problemas mayores, como paradas no programadas o accidentes.
Además de garantizar la seguridad de todos los profesionales, la revisión periódica también ayuda a mantener los niveles de productividad de la empresa.
Imagine que un pequeño daño en el sistema ha pasado por alto en el ajetreo de la rutina. El defecto fue empeorando hasta que provocó que el dispositivo fallara.
Cuando ocurre una situación como esta, se debe detener la producción para averiguar qué causó la falla y luego buscar una solución adecuada.
El tiempo perdido aquí ya es largo, pero aún puede extenderse si es necesario cambiar piezas o incluso reemplazar la maquinaria, lo que aumenta el tiempo de inactividad.
Nadie quiere que la productividad de la industria se vea perjudicada de esta manera, ¿verdad? Ahí es donde entra el mantenimiento preventivo.
¿Qué tan importante es el mantenimiento preventivo?
Mucho más allá de los puntos destacados anteriormente, la inclusión de prácticas preventivas en la planificación operativa de la industria es fundamental para la operación y conservación de los equipos.
El análisis periódico proporciona una visión más clara del rendimiento de los sistemas y, a partir de ahí, es posible definir las fechas de cierre de la fábrica sin interferir con la producción.
Los resultados indicarán la urgencia o no de los procedimientos de parada, permitiendo una planificación eficiente y evitando imprevistos.
Vea cómo la prevención contribuye a la gestión de su empresa en general:
- máximo aprovechamiento de las máquinas;
- mayor seguridad en el manejo;
- prolongación de la vida útil de la maquinaria;
- reducción de costos de reparación;
- evita una caída en la productividad.
El parque industrial brasileño
La industria brasileña está pasando por un momento de renovación. Las últimas décadas han traído varias innovaciones tecnológicas; el enfoque actual, por ejemplo, es la digitalización de procesos.
Sin embargo, el parque industrial brasileño no ha seguido de cerca este movimiento y aún necesita ser actualizado.
Reemplazar máquinas y métodos obsoletos con alternativas más eficientes es una demanda real.
Los clientes quieren un servicio personalizado, productos de calidad, entrega rápida y precios asequibles.
Para ello, es fundamental producir lean (lean manufacturing), haciendo mucho con pocos recursos.
El Gobierno Federal ha lanzado proyectos para incentivar la innovación y el uso de nuevas tecnologías, como el Internet de las Cosas (IoT).
Sin embargo, no basta con adoptar equipos sofisticados si los procesos se mantienen obsoletos. El mantenimiento es una herramienta indispensable para una producción saludable.
Ventajas del mantenimiento preventivo
El mantenimiento preventivo puede entenderse como un sistema para automatizar el seguimiento de los equipos de producción.
El objetivo es dejar de lado la acción correctiva, en la que las acciones son responsivas y se basan en la idea de reparar el daño.
En el mantenimiento preventivo lo ideal es anticiparse a las fallas y evitar que sucedan.
Los beneficios son muchos, empezando por aumentar la eficiencia operativa de toda la organización.
Los indicadores de rendimiento como el tiempo medio entre fallas (MTBF) y el tiempo medio de reparación (MTTR) tienden a disminuir, lo que significa que las máquinas funcionan más tiempo y tienen menos averías.
Otro punto a destacar es la importante reducción de costes que este tipo de mantenimiento es capaz de promover.
Para empezar, el impacto del tiempo de inactividad se reduce ya que los trabajos se programan para pausas de producción.
Además, la reposición de insumos en el stock se mantiene en horario, es decir, se compran menos repuestos en una situación de emergencia.
Con el mantenimiento funcionando al ritmo adecuado, las horas extraordinarias también tienden a disminuir y la vida útil de los equipos y máquinas se prolonga, lo que promueve mejoras en la salud financiera de la empresa.
Desventajas del mantenimiento preventivo
A pesar de tener numerosas ventajas, el mantenimiento industrial preventivo tiene algunos puntos negativos que es necesario tener en cuenta.
Uno de los más fuertes está relacionado con los costos involucrados en el proceso. La prevención requiere herramientas específicas y profesionales cualificadas para llevar a cabo la evaluación.
Por lo tanto, es fundamental realizar un análisis financiero antes de planificar acciones preventivas, plantear gastos estimados y considerar el presupuesto de la empresa.
Otro punto de atención es la planificación.
Cuando no está bien diseñado, el plan preventivo puede tener el efecto contrario y provocar retrasos en la producción o incluso una reducción en la calidad de los servicios.
¿Cuáles son los principales tipos de fallas en los equipos industriales?
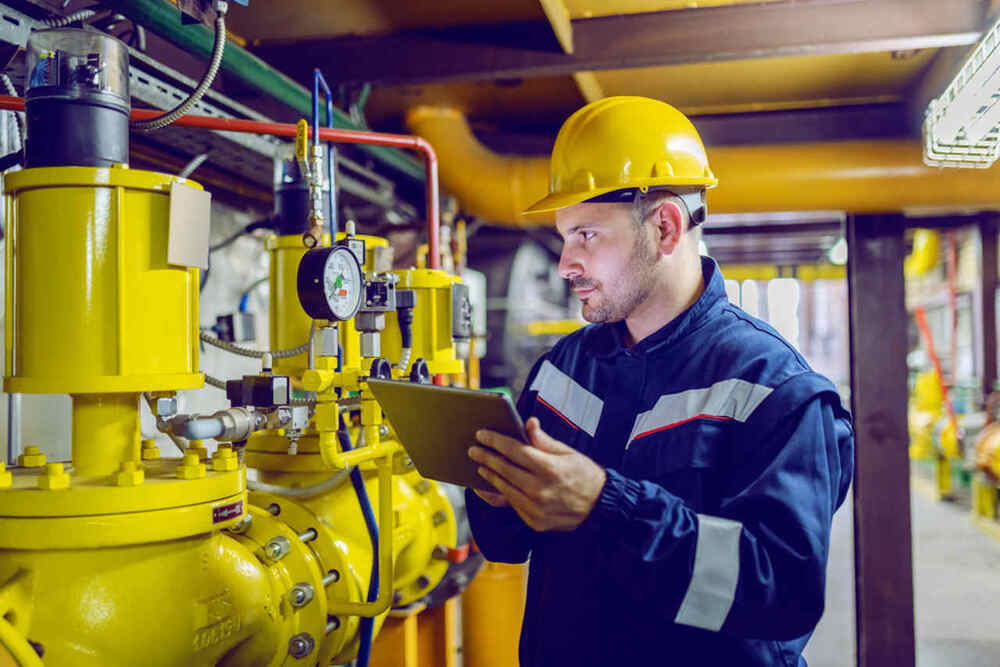
Hay dos tipos principales de fallas en equipos industriales que se consideran indicadores importantes para la prevención: funcionales y potenciales.
Las máquinas no dejan de funcionar de la noche a la mañana, suelen dar algún indicio de que algo anda mal en el sistema.
Estas son las señales a las que los gerentes y empleados deben prestar atención en el día a día de la fábrica. Identificarlos es un paso importante hacia la prevención de daños.
Comprender los conceptos de fallas funcionales y potenciales es parte de esta observación y ayuda a evitar muchos problemas operativos.
A continuación, hemos preparado una explicación de los dos términos para facilitar la comprensión.
Falla funcional
La falla funcional ocurre cuando el equipo no logra alcanzar su nivel máximo de rendimiento.
En este tipo de falla, la máquina continúa trabajando, pero es posible identificar una caída significativa en la productividad en la ejecución de sus funciones.
Es muy común que estos problemas estén relacionados con errores en el proceso de instalación o mantenimiento, así como con el mal funcionamiento de la maquinaria.
Vea algunos ejemplos de fallas funcionales:
- cojinete roto;
- rotura del sello mecánico;
- pérdida de presión o flujo;
- sobrecarga que conduce al disparo del motor.
Si la falla no se resuelve, el empeoramiento del problema puede conducir a la falla del equipo.
Falla potencial
La falla potencial caracteriza el comienzo de un defecto. Son aquellas señales de que algún sistema o parte no está funcionando con normalidad.
Estos son los ejemplos más comunes de este tipo de falla industrial:
- aumento de la temperatura;
- altos niveles de vibración;
- caída en el flujo o la presión;
- aumento de los niveles de ruido de los equipos.
Este tipo de falla puede ser más difícil de identificar, ya que representa una etapa anterior. Sin embargo, cuando se verifica, hace que el mantenimiento sea mucho más simple y económico.
Para que esto sea posible, es necesario contar con un equipo preparado para observar diariamente cualquier cambio en el desempeño de los equipos, aunque sea mínimo.
Mantenimiento preventivo y correctivo: ¿cuáles son las diferencias?
El mantenimiento correctivo tiene un objetivo diferente al método preventivo. Mientras que la prevención actúa en la identificación temprana de fallas, la corrección actúa cuando el problema ya se presentó.
Es decir, el mantenimiento correctivo es la última etapa del cuidado de un equipo, realizado sin una planificación previa.
Este tipo de revisión ocurre cuando algún daño ya está afectando el funcionamiento de la máquina de alguna manera.
La función del proceso es, por tanto, identificar la causa y aplicar la solución más adecuada.
En la mayoría de los casos, el mantenimiento correctivo cubre problemas en etapas más graves, por lo que tiene costos más altos.
Uno de los objetivos del mantenimiento preventivo es precisamente reducir, o incluso eliminar, la necesidad de métodos correctivos, reduciendo los gastos con estas acciones.
¿Cuál es la diferencia entre mantenimiento predictivo y preventivo?
El mantenimiento predictivo y preventivo son acciones complementarias, pero como una diferencia importante entre ellos.
Como hemos visto, el proceso preventivo se realiza en fechas programadas, siguiendo un plan previo.
En el caso del mantenimiento predictivo, no existe un cronograma a seguir. Lo que sucede en este procedimiento es un monitoreo constante del desempeño de las máquinas.
Esto sucede tanto a través de la observación de los profesionales, que deben estar debidamente capacitados para identificar las posibles fallas en el día a día, como a través de recursos específicos.
Un gran ejemplo de estas características son los sensores de temperatura, que monitorean las variaciones y ayudan a detectar niveles irregulares para esa maquinaria en particular.
A pesar de esto, este tipo de mantenimiento sigue siendo muy ventajoso y debe considerarse una inversión.
Incluso con costos más altos, la prevención ayuda a reducir otros gastos. Con una buena planificación, aumenta la calidad de los servicios y la productividad, lo que contribuye a aumentar la rentabilidad.
Curva PF y mantenimiento preventivo: ¿cómo se relacionan?
La Curva PF tiene la función de trazar la predicción de la caída del rendimiento de un equipo a lo largo del tiempo.
Es literalmente una curva, que indica el declive de las máquinas, un proceso natural de cualquier sistema a lo largo de los años.
Para ello, la herramienta considera el intervalo de tiempo entre la falla potencial y la falla funcional, denominado intervalo FP.
En la práctica, funciona como un importante recurso de análisis que sirve de base para evaluar el desempeño de cada máquina según su tiempo de uso.
De esta forma, puede actuar como uno de los indicadores del mantenimiento industrial y auxiliar directamente en la planificación del mantenimiento preventivo.
¿Cuál es el costo del mantenimiento preventivo?
El costo total de la producción industrial varía según la empresa, pero si cuesta más del 5% del valor de sus activos, es una señal de preocupación. Este es un factor clave para evitar pérdidas importantes por daños en los equipos.
Entonces, ¿qué hacer para equilibrar las cuentas? Bueno, el mantenimiento preventivo ya reduce muchos gastos, pero requiere una buena planificación y análisis financiero.
Para planificar los gastos que implica el proceso, es necesario considerar algunos factores, tales como:
- contratación de mano de obra especializada;
- tiempo de inactividad de la máquina;
- necesidad de piezas nuevas;
- inversión en herramientas.
Además de los costos operativos, es necesario evaluar las inversiones en la planificación y gestión del mantenimiento.
Esto incluye estudios para optimizar procesos, uso de tecnologías de automatización y personal para gestionar las demandas relacionadas con este tema.
Criterios para definir la frecuencia de este tipo de mantenimiento
Como hemos visto, el mantenimiento preventivo es periódico, por lo que es importante definir el intervalo entre una inspección y otra a la hora de desarrollar tu planificación.
No existe un estándar para todas las máquinas, el tiempo varía mucho según el modelo, la capacidad operativa de cada una e incluso la rutina de cada fábrica.
Por ello, es necesario hacer una valoración individual de algunos factores a la hora de establecer la frecuencia de este tipo de mantenimiento en tu empresa.
Enumeramos los 4 criterios que pueden servir como base para definir la frecuencia del mantenimiento. Mira cuáles son a continuación.
Recomendación del fabricante
Todos los fabricantes especifican un tiempo recomendado para realizar el mantenimiento, por lo que el primer paso es consultar esta directriz en el manual.
Puede que no sea su criterio definitorio, pero siempre es un factor importante a considerar en las revisiones.
En cualquier caso, presta atención a las indicaciones del fabricante, tanto sobre la frecuencia de las revisiones como sobre cómo se debe hacer en la práctica.
Consultar lineamientos de montaje y desmontaje de piezas para inspección, así como limpieza y productos que pueden o no ser utilizados.
Esta simple acción evitará que se dañen los componentes, lo que podría ocasionar un mantenimiento correctivo más costoso.
Tiempo de funcionamiento del equipo
¿Recuerdas la curva PF? Pues es un factor importante y puede ser el principal criterio a tener en cuenta a la hora de definir el tiempo entre un mantenimiento y otro.
Además de indicar el nivel de rendimiento esperado de la máquina después de ese tiempo determinado de uso, determina ese intervalo entre la falla potencial y la falla funcional.
Con esta información, puede programar el mantenimiento dentro de este intervalo.
Aún hablando del tiempo de funcionamiento, es importante ir más allá de la vida útil del equipo y también evaluar diariamente el período de uso de la máquina.
Un sistema que pasa 8 horas al día funcionando tiene diferentes necesidades que uno que funciona solo 2 horas.
En este caso, define un total de horas trabajadas para el próximo mantenimiento a realizar.
Volumen de producción de la máquina
El criterio de volumen de producción considera una cantidad específica de artículos que la máquina puede fabricar antes del mantenimiento.
Por ejemplo, la máquina X puede producir 8000 artículos antes de que se requiera una inspección, mientras que la máquina Y puede producir alrededor de 1000 productos.
Todo esto debe especificarse en la planificación para evitar confusiones y problemas en el intervalo entre mantenimientos.
Combinación de criterios
Otra opción es combinar dos o más de los criterios anteriores. Puede, por ejemplo, tener en cuenta las directrices del fabricante y el tiempo de funcionamiento de la máquina a diario.
Independientemente de la elección, es importante dejar muy claros los parámetros en la planificación y seguimiento de los resultados.
Las 4 actividades de mantenimiento preventivo
El análisis del desempeño de los equipos requiere de algunos cuidados específicos para que sea posible identificar fallas con anticipación, evitando así mayores daños a largo plazo.
En este contexto, podemos dividir el mantenimiento preventivo en 4 actividades principales para organizar la inspección. Mira cuáles son:
- inspección sensible : el primer paso se realiza desde los sentidos (tacto, olfato y vista), con el objetivo de identificar posibles fallas y daños más claros;
- inspección instrumental : aquí la inspección es más profunda, en la que el técnico utiliza equipos para medir los parámetros operativos del equipo;
- limpieza : después de la inspección, el técnico debe limpiar el equipo, lubricar las partes móviles y volver a apretar los componentes;
- Reemplazo de componentes: si es necesario, el profesional debe reemplazar las piezas defectuosas o desgastadas de por vida.
Conocer estos pasos es fundamental para definir un plan de mantenimiento eficiente enfocado a prevenir fallas.
¿Cómo crear un plan de mantenimiento preventivo?
Como dijimos, el mantenimiento preventivo requiere planificación, pero muchos gerentes tienen dudas sobre cómo configurar este plan de manera eficiente.
Desarrollar un buen plan de mantenimiento preventivo es fundamental para reducir costos, optimizar el proceso de revisión y garantizar la calidad del servicio.
Con eso en mente, hemos enumerado algunos consejos que te ayudarán a la hora de definir tu planificación. Compruébalo a continuación:
- hacer un levantamiento de todas las máquinas en operación en la industria;
- establecer la frecuencia de mantenimiento para cada uno de ellos;
- analizar costos y establecer un presupuesto;
- hacer una lista de verificación de mantenimiento.
Además de planificar la ejecución, es importante pensar en el seguimiento de las acciones preventivas para evaluar si los resultados del proyecto están siendo relevantes.
Para ello, estructure indicadores de desempeño de acuerdo a las necesidades de su empresa.
Consejos para realizar el mantenimiento preventivo
1. Contar con proveedores de confianza
Los proveedores no pueden ser simplemente una fuente de fondos, deben ser socios de su empresa.
No importa qué tan efectivo sea su equipo de mantenimiento de rutina, el retraso en la entrega de piezas, la variación de precios y los materiales de mala calidad pueden romper totalmente su cronograma.
Por lo tanto, encuentre proveedores confiables, involúcrelos en los procesos de reabastecimiento y mantenga asociaciones saludables.
Una buena relación representa la base de un mantenimiento preventivo eficiente.
2. Crea listas de verificación
Cada empresa tiene su enfoque de producción y, en consecuencia, sus exigencias de mantenimiento (mecánicas, eléctricas, lubricación, seguridad, etc.).
Evitar que el servicio se base en el sentimiento de los técnicos es algo que depende de la planificación.
Por lo tanto, comience por establecer una lista de verificación de mantenimiento, es decir, una lista de verificación de los elementos que se revisarán durante las inspecciones.
El control de estos documentos marcará el ritmo de trabajo del sector.
3. Crea horarios y mapea procesos
Tan importantes como las listas de verificación son los programas de mantenimiento. Después de todo, saber qué revisar no es suficiente, es esencial establecer plazos y reevaluar periódicamente cada equipo.
De esta forma, todas las líneas se mantienen dentro de un ciclo de inspección monitorizado.
Por muy experimentados que sean los responsables de las inspecciones, es importante garantizar un nivel de calidad estandarizado. Para ello, mapee los procesos
de cada checklist: defina cada elemento a verificar y cree documentos que detallen cómo se debe realizar esta verificación.
Ejemplos de mantenimiento preventivo
Para integrar los aprendizajes de este artículo, nada mejor que traer ejemplos prácticos de mantenimiento preventivo, ¿no?
Como hemos visto, el proceso consiste en un mantenimiento programado, por lo que no suele incluir aquellas reparaciones más serias, como en el mantenimiento correctivo.
Aquí, el enfoque está en identificar posibles fallas o daños que pueden empeorar con el tiempo y tener consecuencias más graves, afectando el rendimiento de la máquina.
En este contexto, vea algunos ejemplos de este tipo de mantenimiento:
- limpieza de componentes o de la máquina en general;
- lubricación de piezas y partes móviles;
- sustitución de piezas desgastadas;
- aprietes de tornillos;
- pequeños ajustes.
¿Es la hoja de trabajo de mantenimiento preventivo una buena opción?
Si estás pensando en llevar un plan de mantenimiento preventivo en Excel, pero te preguntas si es una buena opción, la respuesta es la que no siempre nos gusta leer: depende.
La hoja de cálculo es una buena herramienta, pero hoy en día es posible encontrar recursos mucho más modernos y eficientes para centralizar datos.
Con esto, evita la molestia de administrar varias hojas de cálculo y puede optimizar los procesos utilizando soluciones de automatización, por ejemplo.
Si lo prefiere, puede utilizar una ficha de mantenimiento preventivo como complemento a las acciones de control, pero merece la pena invertir en tecnologías que faciliten la gestión de la calidad.
El sistema ERP es un buen ejemplo de estas tecnologías habilitadoras, de las que hablaremos con más profundidad a continuación.
Cuente con un ERP para el mantenimiento preventivo
La tecnología es un diferenciador que no se puede ignorar. En mantenimiento, el volumen de información a manejar es demasiado grande para ser respaldado por documentos impresos u hojas de cálculo. El papel del ERP
es precisamente centralizar estos datos, optimizando tanto la gestión como la ejecución de las órdenes de trabajo.
Además, el sistema ERP integra datos de mantenimiento con otros sectores.
Es decir, el uso de las piezas se contabilizará en el stock y la reposición se podrá planificar con mayor precisión.
Por lo tanto, es una solución tecnológica que facilita la rutina de los involucrados con el proceso.
Tecnologías TOTVS para la fabricación
¿Te imaginas centralizar varias funciones en un solo lugar, desde la gestión de inventario hasta el mantenimiento? ¡Con TOTVS Technologies for Manufacturing esto es posible!
Con ellos, es posible enfocarse en mejorar los procesos, a través de la automatización de líneas de producción, gestión de indicadores de desempeño y, por supuesto, el mantenimiento de activos y flotas.
Los sistemas están integrados de punta a punta, con soluciones completas para pequeñas, medianas y grandes empresas.
Como ves, el mantenimiento preventivo ya es una realidad.
Ponga a su empresa en el camino de la Industria 4.0 e invierta en esta estrategia que puede elevar el nivel de calidad de su producción.
¡En poco tiempo, los resultados serán evidentes! ¡Entra en la era de la Industria 4.0 con TOTVS Manufactura!
Conclusión
A lo largo de este contenido, comprendemos cómo funciona y la importancia del mantenimiento preventivo para la preservación de los equipos, la reducción de costos y el máximo aprovechamiento de las máquinas.
En la práctica, el concepto exige una buena planificación para definir la frecuencia del mantenimiento.
Para ello, existen algunos criterios que deben ser considerados como base para identificar el intervalo adecuado entre una inspección y otra.
Además de estos puntos, revisó consejos importantes para configurar su plan de mantenimiento y descubrió cómo la tecnología puede ayudarlo en el proceso.
La prevención es una inversión fundamental para la productividad de la industria, por lo que trata de incluir este tipo de mantenimiento en tus operaciones de la mejor manera posible.
¿Te gustó el mensaje? ¡Así que siga nuestro blog para obtener más información sobre otros temas que pueden ser útiles para su empresa!
Deja tu comentario