La digitalización industrial es una revolución silenciosa que ha transformado procesos, que antes eran manuales, en operaciones ágiles e inteligentes que impulsan la eficiencia y la innovación.
Enfatizamos aquí que no se trata solo de adoptar nuevas herramientas, sino de un cambio estructural, una parte fundamental del concepto de Industria 4.0.
A partir de esto, es muy importante que las empresas se adelanten y levanten esta bandera, es decir, saber qué tecnologías están dando forma a esta transformación y también cómo se pueden aplicar para generar resultados tangibles.
¡Entendámoslo ahora!
Los beneficios de la digitalización industrial
El mercado de la transformación digital continúa a un ritmo acelerado, y las estimaciones señalan que el valor del sector, de alrededor de US$ 911.2 mil millones en 2024, debería alcanzar la impresionante cifra de US$ 3,289.4 mil millones para 2030.
Los datos provienen de la encuesta Digital Transformation Market Size & Share Analysis de Markets and Markets. Este crecimiento interanual del 23,9% refleja el creciente uso de tecnologías avanzadas para satisfacer las crecientes expectativas de los clientes en cuanto a agilidad, eficiencia e innovación.
La digitalización industrial promete una serie de beneficios que van más allá de la simple automatización de procesos.
Las industrias pueden, por ejemplo, alcanzar niveles sin precedentes de eficiencia operativa. Además, la reducción de costos es un factor importante, ya que los procesos optimizados reducen el desperdicio y mejoran el uso de los recursos.
Pero no se trata solo de economía. La digitalización también refuerza la seguridad al reducir el riesgo al minimizar la intervención humana en zonas peligrosas.
Los datos, informes y paneles de control en tiempo real también permiten a los gerentes y líderes realizar un seguimiento de los indicadores de rendimiento y actuar con rapidez, ya que utilizan información más precisa para guiar las estrategias de producción e inversión.
Piense en una línea de producción en la que los sensores de IoT supervisan las máquinas en tiempo real e identifican los fallos antes de que se vuelvan críticos.
Lejos de mantener los equipos funcionando sin problemas, esta práctica también extiende la vida útil y, por lo tanto, genera ahorros considerables para las empresas.
Procesos que se pueden digitalizar en este ámbito
En la práctica, algunos procesos pueden aprovechar muy bien este momento y dar el salto digital.
Los procesos y actividades en áreas como el control de calidad, la logística interna y el mantenimiento predictivo representan oportunidades de optimización que, cuando se adoptan, contribuyen significativamente a la competitividad de la empresa.
Imaginemos, por ejemplo, una fábrica de componentes electrónicos que decide modernizar su control de calidad.
Antes, cada placa de circuito pasaba por una larga inspección manual y estaba sujeta a errores humanos. Ahora, la compañía implementa estaciones automatizadas equipadas con cámaras de alta resolución y algoritmos de inteligencia artificial.
Así, cada placa se analiza en segundos, identificando micro defectos, soldaduras en frío o componentes extraviados con una velocidad y precisión muy superiores a las de la verificación humana.
Esto libera mano de obra para tareas más valiosas y también mejora considerablemente la calidad de los productos.
Tecnologías que se pueden implementar en la industria
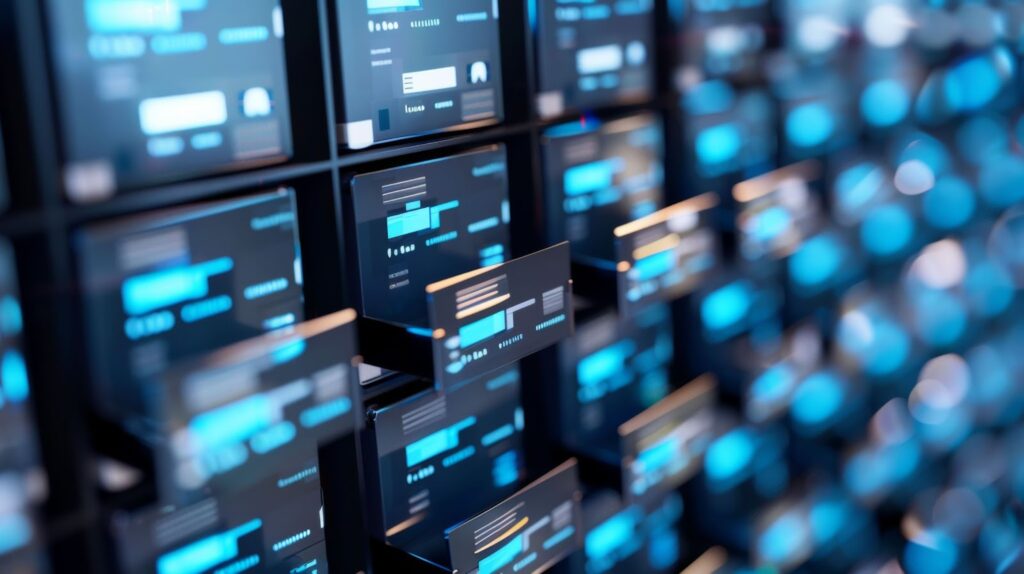
Además de los procesos, es importante destacar objetivamente qué tecnologías se pueden implementar de cara a la digitalización industrial.
¡Conozcamos algunos!
Realidad Aumentada (RA)
La Realidad Aumentada se ha convertido en un poderoso recurso para la industria 4.0, ya que permite superponer información digital al mundo físico.
En las líneas de producción, por ejemplo, es posible guiar a los empleados con instrucciones visuales sobre el montaje o las reparaciones, reduciendo el tiempo de formación y minimizando los errores humanos.
Además, la RA ayuda a los equipos de mantenimiento a identificar los problemas de la máquina más rápidamente, gracias a las instrucciones paso a paso y a las visualizaciones en tiempo real.
Robots autónomos
La adopción de robots autónomos, incluidos los cobots (robots colaborativos), ha crecido significativamente. Estas máquinas realizan actividades repetitivas, pesadas o peligrosas, liberando mano de obra humana para funciones estratégicas.
En la práctica, pueden mover materiales dentro de la planta de producción con precisión, realizar soldaduras en puntos específicos e incluso trabajar codo con codo con los operadores, optimizando todo el ciclo de producción.
Grandes datos
El análisis de big data es la base para una toma de decisiones más inteligente. A través de herramientas avanzadas de análisis e inteligencia artificial, las industrias pueden extraer información que guía todo, desde la elección de las materias primas hasta la previsión de la demanda.
La capacidad de identificar patrones de consumo y rendimiento en tiempo real permite ajustes rápidos en la producción, reducción de desperdicios y una mayor competitividad.
Computación en la nube
La computación en la nube hace posible que las empresas almacenen y accedan a datos desde cualquier lugar, sin necesidad de grandes inversiones en infraestructura física.
Además de reducir los costos, la nube garantiza la escalabilidad, que es vital para mantenerse al día con los picos de demanda. Las actualizaciones de software también se vuelven más ágiles y permiten a los equipos trabajar con la última versión de los sistemas de gestión y las aplicaciones industriales.
Internet de las cosas (IoT)
El IoT conecta máquinas, sensores y dispositivos a Internet, generando un flujo continuo de información sobre el estado de cada equipo.
Esto permite prácticas como el mantenimiento predictivo, en el que es posible identificar y corregir posibles fallos antes de un tiempo de inactividad no planificado. También son posibles mejoras en la logística interna, con seguimiento en tiempo real de los artículos y optimización del movimiento de la carga.
Impresión 3D
La fabricación aditiva, conocida popularmente como impresión 3D, ha revolucionado la forma en que se producen piezas y prototipos.
Además de acelerar el desarrollo de nuevos productos (ya que el prototipo se puede crear en horas, no en semanas), la tecnología permite una mayor personalización y, en algunos casos, una producción bajo demanda.
Esto reduce los costos de inventario y hace que la línea de producción sea más flexible y adaptable a los requisitos del mercado.
Sistemas integrados de gestión
La integración de datos y procesos a través de sistemas de gestión (ERP, MES, WMS, entre otros) es fundamental para monitorear cada etapa del flujo de producción.
Con un ERP robusto, por ejemplo, la empresa centraliza la información sobre compras, ventas, inventario y finanzas en una sola plataforma, lo que garantiza una visibilidad completa de las operaciones.
Esta integración optimiza la toma de decisiones, facilita la comunicación entre equipos y mejora la previsibilidad de los resultados, creando una base sólida para la transformación digital.
¿Cuáles son los retos de la transformación digital en la industria?
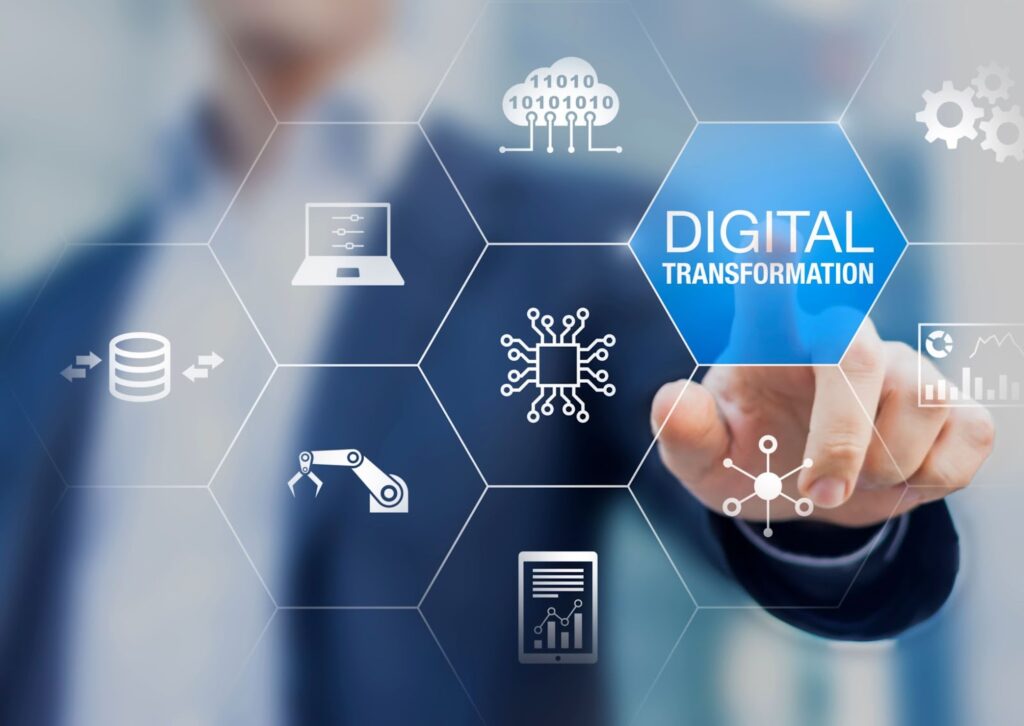
Según el IBGE, el 80,8% de las medianas y grandes empresas industriales señalan los altos costos de las soluciones tecnológicas como la principal barrera para avanzar en la digitalización.
Este factor se vuelve aún más crítico cuando se considera que los proyectos de automatización e integración de sistemas suelen implicar fuertes inversiones, tanto en infraestructura como en capacitación y adaptación de procesos.
Otra dificultad llamativa revelada por Pintec Semestral 2022 es la escasez de profesionales calificados.
Según la encuesta, el 54,6% de las empresas se enfrenta a la falta de personas preparadas internamente, mientras que el 48,9% cita la escasez de mano de obra especializada en el mercado como un obstáculo importante.
Sin equipos que dominen tecnologías como el IoT, el análisis de datos, la automatización y la ciberseguridad, la implementación de soluciones digitales tiende a ser más lenta y costosa.
Todavía hay problemas estructurales, como la provisión de conectividad de calidad, la resistencia cultural al cambio organizacional y la necesidad de una gobernanza de datos eficiente para respaldar la adopción de nuevas herramientas.
Para superar estos obstáculos, es fundamental invertir en formación profesional, buscar líneas de financiación e incentivos que hagan más accesibles las tecnologías, además de promover una cultura de innovación que involucre a todos los niveles organizativos.
¿Cómo ayudan los productos TOTVS en la digitalización industrial?
Los productos de TOTVS han sido protagonistas en este viaje de digitalización, entregando soluciones integradas que agilizan la gestión y el análisis de datos.
Al tratarse de un conector de gran tamaño, estas soluciones centralizan los procesos y garantizan una mayor eficiencia y control de las operaciones.
Conclusión
¿Estás listo para impulsar tu negocio en la era digital?
Esta es una parte importante de la agenda de aquellos que quieren crecer en este mercado en constante evolución.
Al adoptar tecnologías como la realidad aumentada, el IoT y los sistemas de gestión integrados, las empresas ganan agilidad, reducen costes y aumentan su capacidad de innovación.
Sin embargo, para obtener resultados reales, es fundamental contar con socios sólidos y herramientas adecuadas, como las soluciones TOTVS, que simplifican los procesos y garantizan una mayor confiabilidad de los datos.
Así, ya sea en el control de calidad, la logística interna o la integración de áreas de negocio, la digitalización industrial se convierte en la base para el crecimiento sostenible y la conquista de nuevos mercados en la industria.
Deja tu comentario